I sat down with some engineers today before sitting down to
type up my blog post. I wanted to find out some
of the main causes for voltage noise in our supplies so that I can share it with you Watt's Up readers. Please note that each of these reasons could
be a blog post of its own but for brevity's sake I am going to come at this for a high level. Since our
newest supplies have the high power density, they are mostly switch mode power supplies. The top cause of noise in switch mode power supplies is the frequency of the switching inverters. This is inherent to the design of the supply. The second most
common cause of noise is common mode current noise that turns into
normal mode voltage noise. We have
filtering and common mode chokes inside the supplies but some still gets through and
comes out the output as normal mode voltage. The
third most likely cause is noise from operational amplifiers that makes its way
to the outputs. After talking to our
designer I came out with a new respect for the challenges they face when having
to deal with this!
I recently did a video on how to make this measurement:
I wanted to use the Watt’s Up blog to add some more information.
The general schematic for noise testing is:
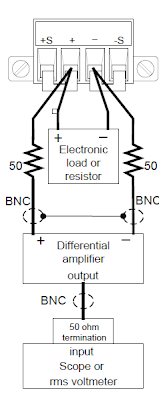
One thing that I wanted to do in the video but was not able
to for brevity’s sake was talk about the differential amplifier. The differential amplifier is important for
two key reasons. The first reason is
that the differential amplifier will greatly reduce the common mode noise on
the output. This is important because
you want to measure the noise between the outputs. The other benefit of the differential amplifier is that it multiplies the output by 10. This multiplication enables
us to use more accurate ranges in both the scope and the RMS voltmeter which is very important when you want to keep the measurement uncertainties of your measurements down.
When you do the noise test, typically you do it at the full power
point. To get the full current, you can
either use an electronic load or a fixed resistor. Typically on a lower noise supply (such as
the N6761A) you want to use a fixed resistor since the electronic load will
introduce its own noise to the measurement.
This is not really an issue for power supplies with higher noise because
their output noise is higher than the noise from the load. In all honesty, it also tends to be difficult to find 500 W
resistors so the load is a great help in those instances too!
The last measurement item that I want to talk about is the scope setup. The scope should be AC coupled and
have the filter turned on (since we only specify noise to 20 MHz, we
want to filter anything above this out). We recommend that you put the scope in peak
detect mode and turn the statistics so that you can see the highest and the
lowest voltages recorded. This will give
you the true variation in the power supply output. Your peak to peak voltage noise will be this
difference divided by the gain of the diff amp. After taking the peak to peak measurement, I typically move the connector over to the RMS voltmeter to take that measurement. There are no special settings for the RMS voltmeter, you just need to remember to divide by the gain of the differential amplifier.
That is a really quick overview of voltage noise. Please feel free to leave any questions in the comments section of this blog.